Digital twins in manufacturing:
Examples and use cases
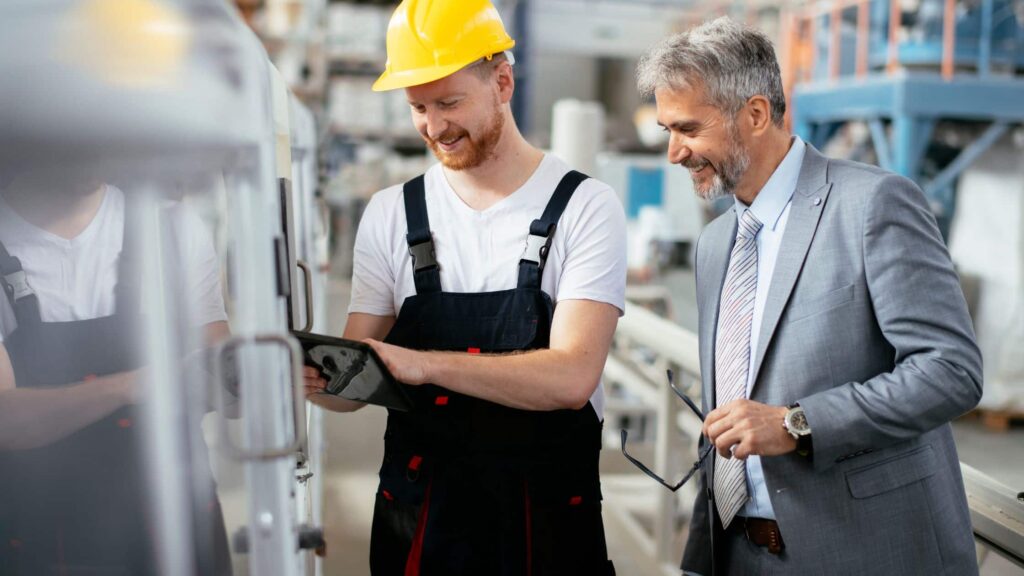
With every year that goes by, the use of digital twins is being adopted more and more by different industries. From metals and engineering to food manufacturers, energy, forestry and chemicals, the number of use cases and needs is almost as great as the number of industries and actors.
Process Genius has a long experience in industrial environments and we have seen over the years that in many cases the needs of industrial operators culminate in production cost control, efficient resource allocation and day-to-day management.
Are you wondering how the digital twin could be the cornerstone of your production and day-to-day management? In this article, we share real-life examples and use cases of how other leading companies in the manufacturing and process industries are using the digital twin to improve their own production, competitiveness and day-to-day management.
Examples and use cases of how digital twins are used in manufacturing and process industries
Predictive maintenance
Digital twins play a crucial role in predictive maintenance, allowing manufacturers to detect potential equipment failures before they occur, reducing maintenance downtime and improving operational efficiency. Konecranes, the global leader in material handling, uses the Smart Factory Digital Twin platform in its factory to predict and prevent downtime, optimize maintenance schedules and ensure continuous production. In addition, Konecranes offers the Smart Factory solution to its customers as a daily management tool that provides them with a complete view on what is happening in the factory. Read the full customer story.
Production optimization
Digital twins are also used to optimize production processes by observing different scenarios and identifying the most efficient ones. Specializing in light and mid-heavy CNC machining, CNC Machining uses a digital twin to monitor maintenance and maximize production times and use of existing resources, allowing production adjustments to be made to reduce waste. Read the full customer story.
Quality control
The digital twin enables production quality control and monitoring to ensure that products meet defined standards. Snellman, one of Finland’s largest food industry companies, uses a digital twin to monitor cooking processes in real time, allowing immediate adjustments to be made during production to maintain product quality and reduce waste. Read the full customer story.
Data-driven decision-making
The digital twins are used to improve informed decision-making by providing real-time visibility of processes and insights into future scenarios. Stora Enso uses digital twins in its mill sites both in Finland and abroad to aggregate data and gain a clear understanding of the situation in the mills at any given moment, enabling better decision making and predictability. Read the full customer story.
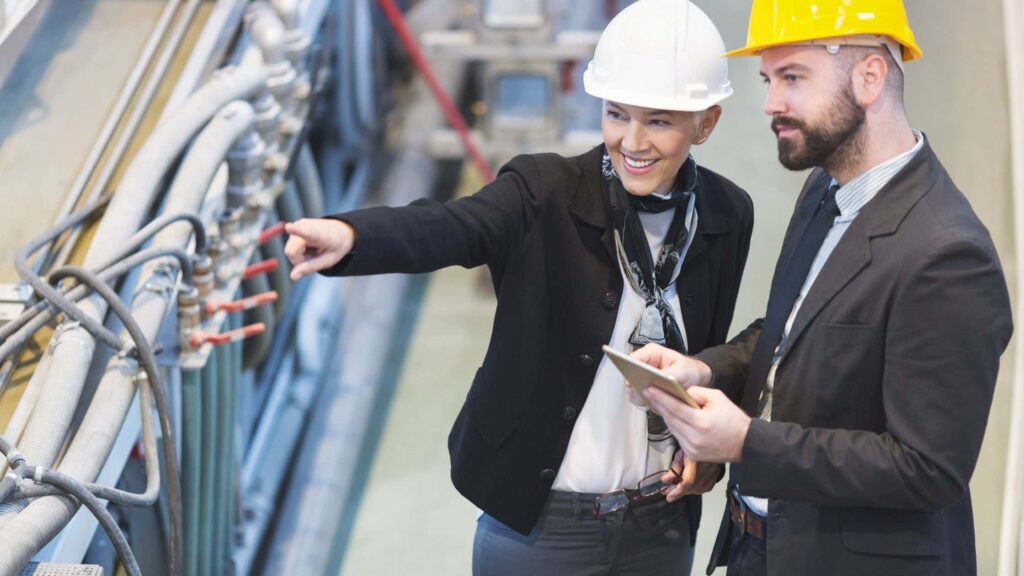
Training and documentation
Digital twins create virtual training environments where workers can practice using equipment and processes in a safe and controlled environment. One company specializing in mineral processing is using the digital twin to train new staff and provide all the necessary information to contract maintenance workers, reducing the risk of accidents and improving overall operational skills. Read the full use case.
Energy efficiency
Digital twins are used to optimize energy consumption and reduce CO2 emissions in manufacturing processes. One company specializing in the manufacture of plastic parts, uses a digital twin to monitor and analyze the energy use of its production facilities, helping to identify energy-saving opportunities and reduce its environmental impact. Read the full use case.
The future of manufacturing lies in the power of digital twins
Through the real-world examples and use cases presented in this article, digital twins have already made a positive impact in various sectors of manufacturing. For example, machine shop specialists use digital twins in their day-to-day management to monitor equipment lifecycles, allocate resources, perform predictive maintenance and prevent unplanned downtime. Pioneers in the food and other process industries are also using this technology to optimize production and ensure quality.
The future of manufacturing lies in the power of digital twins. With advancements in artificial intelligence and connectivity, these virtual replicas will become even more sophisticated and capable of driving innovation. By embracing the digital twins, industrial companies will gain a competitive advantage in today’s fast-evolving industry.
Whether you are a production manager looking to optimize your production line or an organizational leader trying to stay at the forefront of developments, digital twins are a technology worth exploring. For more information about our 3D Digital Twin solutions for the manufacturing and process industries, please send us a message and we will contact you soon!