The digital twin in industry: how does the digital twin sit alongside ERP, MES and MRP?
Do you know which of your equipment is currently out of order or slowing down your production? Can you reliably identify problems and opportunities for process improvements in your production from a distance? You should.
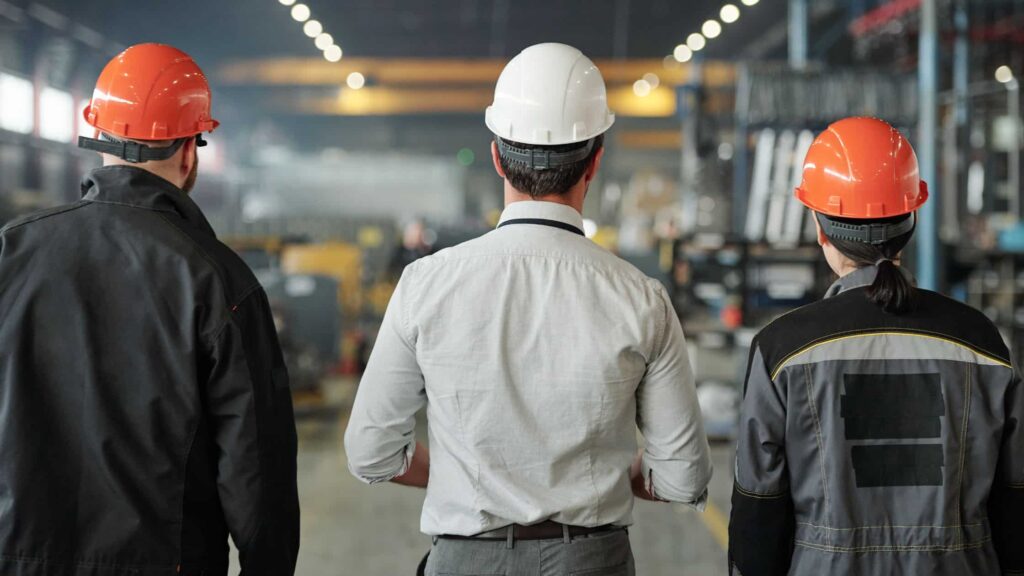
In today’s industrial world, the complexity of production processes, the need for data-driven decision making and the sheer volume of industrial systems and data have required new innovative solutions. We have seen that it is in this context that the digital twin has emerged as a technology of primary importance and popularity.
The digital twin creates a virtual replica of the physical environment or device, providing an accurate and comprehensive view of the real-time and historical data of the device. The aim is to monitor and analyse equipment and processes in real time. When considering in more detail the impact of the digital twin on different production functions, it is also important to understand how it fits into already established industrial systems, the most popular of which include ERP (Enterprise Resource Planning), MES (Manufacturing Execution Systems) and MRP (Material Requirements Planning).
In this blog post, we will summarise in an understandable way the benefits and potential of the digital twin in combination with ERP, MES and MRP systems. We aim to give production experts like you the information you need to use these tools effectively and manage your production with data-driven confidence. At the same time, we get a glimpse of the digital twin’s core functions in enabling predictive maintenance, optimising production processes and driving sustainable business growth.
To refresh your memory – What is a digital twin?
A digital twin is a virtual copy of a physical device, process or environment. The digital twin can monitor and evaluate the performance of its physical counterpart using real-time data from sensors, IoT devices and other sources that monitor the performance of the device. This enables, for example, early identification of problems in equipment performance, predictive maintenance, process optimisation and the identification of potential areas for improvement without having to touch the physical equipment itself.
What is ERP?
An ERP (Enterprise Resource Planning) system is a comprehensive information system that integrates a company’s core business processes and integrates the various data into a single entity. It is used to make decision-making more effective. ERP acts as a central platform for managing different aspects of your business, such as finance, HR, supply chain, procurement, services and customer relationships. The aim of an ERP system is to streamline operations and improve efficiency by providing a single view of a company’s resources and processes.
ERP integrates data from different business processes, digital twin makes them easily visible
What is MES?
A Manufacturing Execution System(MES) is an information system that provides real-time visibility and control of production processes on the shop floor. It monitors and optimises production activities, collects data and provides comprehensive information on performance, status and quality.
MES looks to the present, the digital twin also looks to the future
What is MRP?
MRP ( Material Requirement Planning) is a production planning, scheduling and inventory management system used to manage and control the inventory of materials required for production. It focuses on analysing demand, taking into account the bill of materials and developing a plan to procure or produce materials in a timely manner to keep production efficiently on schedule.
MRP focuses on near-term planning, the digital twin is also excellent at predicting future results
In the future, the digital twin will optimise the use of industrial systems
The digital twin is fast becoming an important part of the day-to-day management of industry. So we can expect even bigger developments and real-life examples of how the digital twin sits alongside ERP, MES and MRP systems – and how it may even be a crucial part of the real business value of these tools. For example, ERP systems are often complex data centres, which requires extensive training and ongoing support to enable employees to use the system effectively. By seeing the whole picture in real time through the digital twin, and only the data that is relevant to your role, your business can save valuable time and resources.
By integrating your ERP, MES and MRP system with the digital twin, you can create a seamless and efficient workflow that maximises productivity and makes day-to-day management easier by creating a clear, reliable overview of the most important monitoring points in your production anywhere, anytime.
If you would like to learn more about our Digital Twin solution for the manufacturing and process industry, drop us a line and we’ll get back to you!