EFM Group wants to know – not guess – the long-term impact of the production
CNC-Machining Oy, a Joensuu-based engineering company, is now part of EFM Group Oy, a consortium of three North Karelia-based engineering companies. All three subsidiaries of EFM Group Oy; CNC-Machining Oy, ViiMet Oy and KKR Steel Oy, are customers of Process Genius.
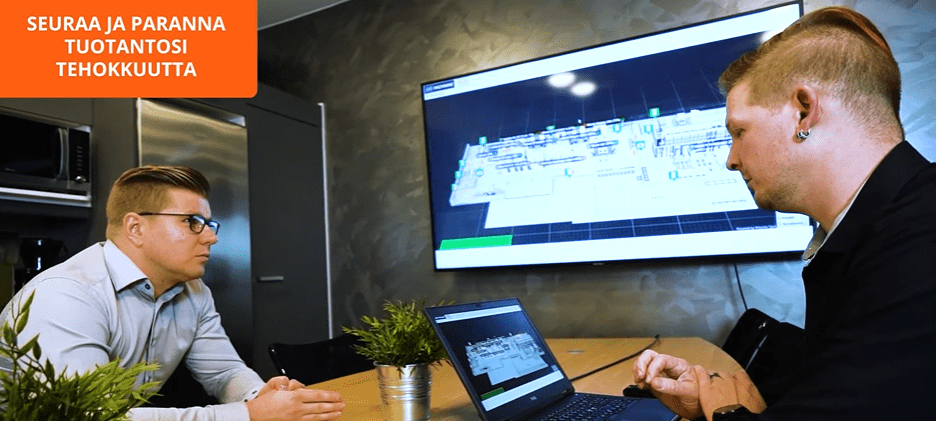
CNC-Machining Oy believes that continuous innovation brings world-class success. The profitability of the operation depends on how much of the actual capacity of the machine is in use. To maximize productive time, a partnership was launched with Process Genius, a provider of Digital Twin services. The new platform opened up the transparency of resource use to management. No longer left to guesswork, a real-time view of the factory is available remotely and from any device.
We aim to make the best use of existing resources. Now, even with limited time and capacity, the required efficiency can be achieved. The digital twin platform enables us to measure the productive time of machines and how much actual capacity is used, as the customer only wants to pay for the finished piece. The price is based on time and resources, which they don’t pay for.”
At CNC, the development principle is grounded in Lean methods of eliminating waste. You only do what the customer is paying for. When a new development is made, we immediately look at the next thing that could be done better. Production is constantly being monitored and better solutions for measurement are being sought. Monitoring has even helped to find differences in production between shifts. It is easy to see how production efficiency can be improved as a result of monitoring and the measures taken as a result.
A digital dashboard ensures that maintenance is really done
In addition to the utilization rate monitoring, the most used function is the maintenance monitoring. “The digital dashboard for maintenance has ensured that the maintenance is actually done. Premature failures can be prevented, and the savings can amount to thousands of euros,” says Herranen. Document management is also made easy with the platform. Quality documents, safety instructions and production-related issues are easy to manage.
Cooperation with Process Genius has gone smoothly, according to Herranen. “The service process was clear. The customer focus was evident in what we did – our opinion mattered and the development went well. We got what we asked for.” According to Herranen, surface treatment companies, small engineering companies and machine repair shops, for example, could benefit from Process Genius’ digital twin solution to monitor the status of their operations.
Investing in continuous development, CNC views itself as a high-quality company in which continuous transparency is important. When asked about their next development targets, Herranen says that it would be interesting to gain more detailed knowledge of how much they can produce at the current utilization rate, and how much unused capacity there is in each production machine.
Other customer stories
Pekotek: White Labeling allows Pekotek’s end customers to benefit from cost savings and predictive maintenance capabilities provided by the 3D Digital Twin
Taking day-to-day management processes to a new level – Konecranes Smart Factory
Working together to develop service business – Flowrox and Process Genius
All the information you need at one glance. One platform.
Want to know more about our solution for your organization? Please drop us a line and we’ll be in touch!