Digital twins in manufacturing – 8 reasons why digital twins are important
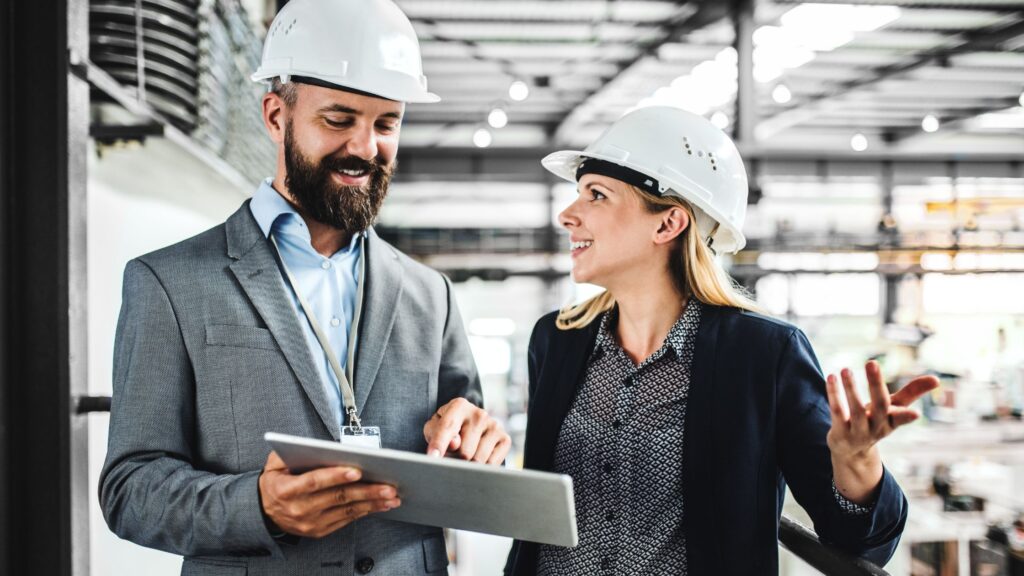
Digital twins are virtual copies of physical objects or processes, brought to life by advanced modelling and simulation techniques. They allow manufacturers to create a virtual environment that simulates the real world, offering many benefits throughout the production, machinery and end-product lifecycle.
In this article, we explore eight key benefits of why digital twins have become key enablers and tools for smart industry, driving operational efficiency, product quality, innovation and cost savings.
According to Altair Engineering’s 2022 Digital Twin Global Survey Report, among others, employees said the most common benefits of digital twin technology were real-time monitoring and control (38%), efficiency and safety (37%), and cost savings (33%). One of the key findings of this study was that 92% of respondents who used digital twin technologies (N=1 393) said it made their products and processes more sustainable.
So, whether you are a manufacturer curious about digital twins or simply interested in the latest advancements in technology, this article is for you.
8 reasons why Digital Twins are needed in manufacturing
1. Improved efficiency
Digital twins provide real-time information that can help improve machine and equipment performance, streamline processes and reduce production downtime. Resource allocation and process optimization are facilitated by scenario simulations.
2. Predictive maintenance
Digital twins can predict potential equipment failures and maintenance needs, enabling predictive maintenance planning. This approach reduces unplanned production downtime, extends machine lifespan and lowers maintenance costs.
3. Improved product development
In product design and manufacturing, digital twins speed up the development process, reduce the need for physical prototypes and improve product performance before mass production.
4. Remote monitoring and control
Digital twins allow companies to monitor and manage assets in difficult or dangerous circumstances, even remotely and in real time. This capability increases security, reduces the need for physical presence and enables remote decision making.
5. Informed decision-making
Digital twins can combine huge amounts of data into a single view that can be analyzed to make informed decisions. Organizations can identify patterns, optimize processes and discover new insights, leading to informed and strategic decision-making.
6. Better cooperation and support for employee training
Digital twins allow all parties involved in production to work together, share information and get an in-depth understanding of the resources or projects at hand. This cooperation encourages better team coordination and communication.
7. Lower costs
By improving the performance of machines and equipment, anticipating maintenance needs and reducing idle times, digital twins help reduce operating and maintenance costs.
8. Sustainable development and environmental impact
Digital twins contribute to sustainable production by improving waste management, reducing energy consumption and improving environmental performance.
Digital twins drive industry towards a more efficient and sustainable future
Digital twins are changing the way industry works, offering significant benefits in all areas of production. By providing real-time data, predictive analytics and virtual testing capabilities, digital twins enable manufacturers to make informed decisions, improve their overall efficiency and deliver superior products to the market. In addition, the ability of digital twins to simulate and model the behaviour of physical assets opens up new opportunities for predictive maintenance, supply chain optimization and continuous production improvement.
As the industry continues to evolve and embrace digital transformation, the adoption of digital twins will become increasingly important for manufacturers to remain competitive in a rapidly changing market environment. It is therefore imperative that manufacturing organisations adapt and use this technology wisely to stay ahead of the curve and drive their processes towards a more efficient and sustainable future.
Learn more about our Digital Twin solutions for the manufacturing andand process industries, or send us a message and we will contact you!