How IoT, AI, and 3D Digital Twin boost predictive maintenance in manufacturing
In this article, we will explore how IoT, AI, and 3D Digital Twin can work together to improve predictive maintenance, streamline operations, and reduce costs.
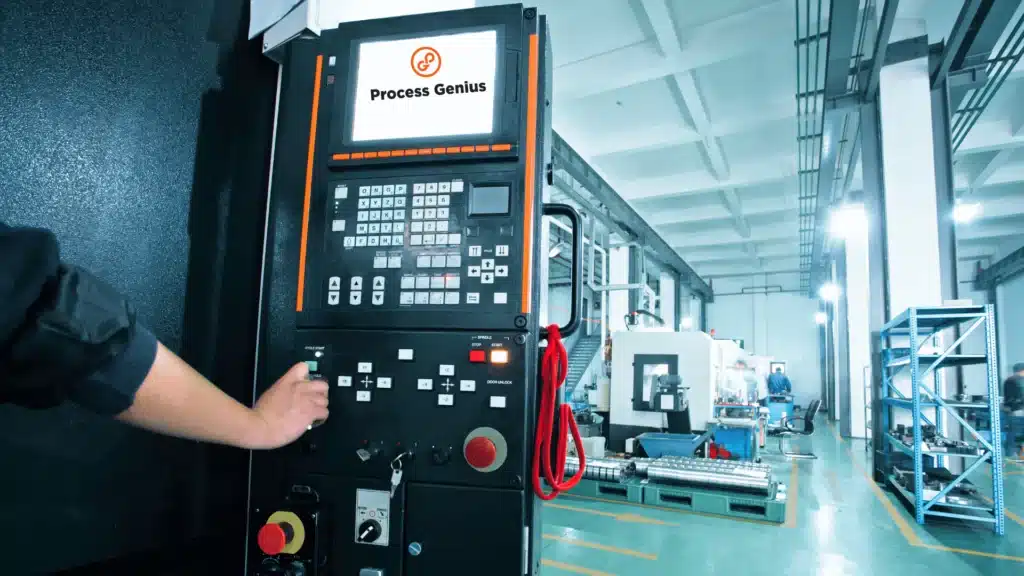
In today’s rapidly evolving manufacturing world, predictive maintenance has become an essential strategy for boosting productivity and cutting costs. While traditional preventive maintenance remains important, it can lead to inefficiencies or unplanned downtime. By leveraging modern technologies like the Internet of Things (IoT), 3D Digital Twin, and AI, predictive maintenance enhances preventive efforts, allowing manufacturers to anticipate issues before they arise.
In this article, we will explore how these technologies can work together to improve maintenance, streamline operations, and reduce costs.
What is predictive maintenance in manufacturing?
Before diving into the specific technologies, it’s crucial to understand how predictive maintenance enhances manufacturing. Predictive maintenance is a proactive approach that uses real-time data to anticipate equipment failures before they occur. By continuously monitoring conditions, analyzing historical performance, and identifying trends, manufacturers can predict when breakdowns are likely to happen.
Predictive maintenance strengthens traditional preventive maintenance by optimizing repair timing based on data. Rather than following a rigid schedule, manufacturers can act only when needed, reducing maintenance costs and downtime while extending equipment lifespan.
In addition to improving preventive maintenance, predictive strategies minimize unplanned repairs. Sudden failures can bring production to a halt, causing delays and lost revenue. Predictive maintenance enables manufacturers to plan repairs during scheduled downtime, avoiding unexpected interruptions.
The role of IoT in predictive maintenance
The Internet of Things (IoT) plays a game-changing role in predictive maintenance by creating a network of connected devices that gather and transmit data continuously. Sensors embedded in machinery collect crucial performance metrics like temperature, vibration, and pressure in real time. These sensors are linked to the internet, making it easy to analyze and use the data for predictive maintenance.
Key advantages of IoT in predictive maintenance:
- Real-time monitoring: IoT devices constantly track equipment conditions, giving maintenance teams instant insights into how machines are performing. This data is invaluable for spotting small changes in performance that could signal a potential failure.
- Remote monitoring: In large-scale industrial settings, IoT makes it possible to monitor equipment remotely. Maintenance teams no longer need to be on-site to understand the health of their machines, which simplifies managing operations across multiple locations.
- Automated alerts: IoT can automate alerts when something is off. For instance, if a machine’s vibration levels go beyond normal, the system sends an alert to the maintenance team. This allows for quicker intervention, helping to prevent costly breakdowns.
Case Study: Ford’s IoT-driven predictive maintenance
Ford, a leading automotive manufacturer, implemented IoT predictive maintenance solutions to monitor the health of its production-line equipment [1]. The company installed IoT sensors on critical machines, tracking temperature, pressure, and vibration. With the help of real-time data from these sensors, Ford identified early signs of component fatigue and conducted timely repairs.
By using IoT for predictive maintenance in manufacturing, companies could reduce machine failure rates by 25% and cut equipment downtime by 15%. The system also enables more efficient scheduling of maintenance, optimizing production capacity while reducing overall maintenance costs.
3D Digital Twin in manufacturing: Benefits and use cases
A 3D Digital Twin is a virtual model of a physical asset or system, constantly updated with real-time data from the actual environment. It allows manufacturers to monitor and predict how machinery will perform, helping them anticipate when maintenance will be needed.
Key advantages of Digital Twins in predictive maintenance:
- Real-time data: Digital Twins provide an overview of machine operations based on real-time data and offer valuable insights.
- Improved decision making: Maintenance teams can use these virtual models to plan different maintenance strategies before acting. For example, before performing repairs, they can assess the impact of various approaches to ensure the most effective solution is chosen.
- Reduced downtime: By predicting and addressing problems before they escalate, Digital Twins help reduce the risk of unexpected downtime, allowing manufacturers to keep their operations running smoothly and efficiently.
Case Study: Siemens’ Digital Twin in gas turbine maintenance
Siemens, a global leader in engineering, developed a 3D Digital Twin for predictive maintenance of its gas turbines. [2] The Digital Twin simulates the turbine’s operations, capturing real-time data from IoT sensors installed on the physical machine. The combination of real-time sensor data and simulation capabilities allows Siemens to detect potential issues before they escalate into critical failures.
Using the Digital Twin for predictive maintenance, Siemens could reduce unexpected breakdowns by 20% and extend the operational life of its turbines by 10%. This approach leads to significant reductions in maintenance costs and improved overall operational efficiency.
Case Study: Boeing uses Digital Twins for aircraft maintenance
Boeing, one of the largest aerospace manufacturers, implemented a comprehensive predictive maintenance solution based on Digital Twin technologies. It helped to simulate the performance of each aircraft system.
This system has significantly reduced Boeing’s maintenance costs and equipment downtime, enabling the company to achieve up to a 40% improvement in first-time quality of the parts and systems it uses to manufacture airplanes. [3]
The role of AI in predictive maintenance
While IoT devices provide valuable raw data and Digital Twins visualize it, AI-based predictive maintenance takes things a step further by using advanced algorithms to analyze that data to accurately predict when failures might occur. AI can process large datasets from IoT sensors, detecting patterns and trends that reveal potential issues.
How AI enhances predictive maintenance:
- Advanced data analytics: AI can sift through vast amounts of sensor data, analyzing it in real time to spot even the smallest anomalies in equipment performance. This leads to more accurate predictions about when maintenance should be carried out.
- Self-learning models: AI models can “learn” from past performance data. Over time, they get smarter, refining their accuracy as more data is fed into the system. This self-learning feature ensures that predictive maintenance becomes more efficient and reliable as time goes on.
- Automated decision making: AI systems can also automate especially repetitive decision-making processes by triggering maintenance activities when certain thresholds are met. This streamlines routine operations, helping to minimize delays.
Case Study: General Electric’s AI-powered predictive maintenance
General Electric (GE) has integrated AI-based predictive maintenance into its manufacturing processes, using AI to monitor and analyze the performance of engines and turbines. [4] By leveraging AI, GE can predict engine component failures with high accuracy. The AI system processes real-time sensor data from IoT devices to detect anomalies, and alerts maintenance teams when repairs are needed.
This implementation of AI should bring unplanned maintenance down by 30%, significantly cutting repair costs and improving asset reliability.
How IoT, AI and 3D Digital Twin work together to enhance predictive maintenance?
When IoT, 3D Digital Twin, and AI come together, they create a powerful ecosystem that takes predictive maintenance in manufacturing to a whole new level of precision and automation. Each technology brings its own unique strengths:
- IoT delivers real-time data that is crucial for monitoring equipment and gathering insights.
- Digital Twins provide a comprehensive view of the states of different machines, systems and whole production lines, enabling accurate predictions for maintenance needs.
- AI processes the data from IoT sensors, using predictive models to identify potential failures and optimize maintenance schedules.
Together, these technologies form a comprehensive approach to industrial IoT and maintenance, giving manufacturers complete, real-time visibility into their assets. This integration not only drives predictive maintenance cost reduction but also improves operational efficiency and reduces production interruptions. Plus, by anticipating equipment failures long before they happen, manufacturers can significantly cut down on equipment downtime.
Challenges and future trends
Despite the many advantages, there are still some challenges when it comes to implementing these technologies in manufacturing.
Key challenges:
1. High initial costs
Setting up IoT sensors, building Digital Twins, and deploying AI models often requires a substantial financial investment, which can be particularly tough for small and medium-sized manufacturers.
Because of this challenge Process Genius exists. For over a decade, we have been working with some of the biggest names in the manufacturing and process industries, helping them overcome challenges like this. Our Genius Core™ platform is a fully configurable, cost-effective 3D Digital Twin platform designed specifically for industrial needs.
Tackling high initial costs: Our Genius Core™ platform comes with flexible pricing plans that scale with your business needs, making it easier for manufacturers to deploy a 3D Digital Twin without breaking the bank. This flexibility allows businesses to start with a base package and expand as they grow, providing a cost-efficient way to take advantage of advanced digital twin technology while keeping costs under control.
2. Data integration
Integrating IoT data into existing systems can be challenging, especially when older machines were not built for connectivity. In many cases, manufacturers might need to retrofit equipment or invest in modern technology to enable IoT integration.
Easy data integration: One of the standout features of our Genius Core™ 3D Digital Twin platform is how effortlessly it integrates data from various sources. Whether it is data from ERP systems, MES, SCADA, or industrial wireless sensors, the platform brings everything together in a seamless way. This means manufacturers can see real-time data from across their production lines all in one easy-to-use interface, giving them a complete, clear overview of their operations.
Simplifying large data sets: Handling large volumes of data can be overwhelming, but the Genius Core™ 3D Digital Twin platform makes it simple. Users can customize dashboards and reports based on their specific needs, allowing each role—whether it is a production manager, operator, or maintenance team member—to focus on the data that is most relevant to them. This flexibility ensures that everyone gets the information they need, without getting bogged down by unnecessary details, helping businesses avoid data overload.
With the Genius Core™ platform, users can easily upload a 2D or 3D model of their factory, add points of interest (POI) markers, integrate data from sensors, and monitor production status in real time, no matter where they are. Plus, integration with Azure AD makes managing users and access seamless, improving both security and efficiency.
3. Data security
With large amounts of data being sent across networks, cybersecurity is a major concern. Protecting sensitive operational data from unauthorized access or tampering is essential to avoid costly disruptions.
Process Genius tackles this issue head-on by offering robust security through our Genius Core™ platform, hosted on secure cloud services. This SaaS-based solution integrates seamlessly with Azure AD, simplifying user authentication and authorization, while enhancing security with centralized identity management. By hosting on the cloud, our clients benefit from advanced security protocols and continuous monitoring, ensuring that only authorized personnel can access critical production data. This safeguards the platform from unauthorized access and potential breaches, keeping operations running smoothly and securely.
Future trends:
- 5G connectivity: As 5G networks continue to roll out, the speed and reliability of IoT data transmission will drastically improve. This will allow for real-time monitoring and analytics on a much larger scale, making predictive maintenance even more effective. Genius Core™ platform is already fully equipped to leverage 5G connectivity, ensuring faster data processing and improved system responsiveness as this technology becomes more widely available.
- Augmented reality (AR): AR has the potential to transform predictive maintenance by overlaying digital information onto real-world environments. For instance, maintenance teams could use AR to visualize a Digital Twin while working on actual equipment, making repairs faster and more efficient. The Genius Core™ platform already supports integration with AR services, allowing users to interact with their Digital Twin environment through augmented reality, further enhancing operational insights and efficiency.
Conclusion
The combination of IoT, 3D Digital Twin, and AI is completely transforming the way manufacturers approach predictive maintenance. These technologies not only help reduce equipment downtime and lower maintenance costs, but they also drive operational excellence and help future-proof businesses. As they continue to evolve, their impact on the manufacturing sector will only grow, making predictive maintenance smarter, more efficient, and even more cost-effective.
If you would like to learn more about how we can help your business leverage these technologies, or if you have any questions, feel free to reach out to our specialists. We are here to help you take the next step toward smarter, more efficient operations.
Sources:
- [1] Drivers to Benefit from Smarter Insurance, Maintenance and Recovery Following Connected Vehicle Data Collaboration. Retrieved from https://media.ford.com/content/fordmedia/feu/en/news/2020/11/11/drivers-to-benefit-from-smarter-insurance–maintenance-and-recov.html (read September 24 2024).
- [2] Gas turbine simulation software: Design clean and efficient gas turbines. Retrieved from https://resources.sw.siemens.com/en-US/solution-brief-gas-turbine-simulation-software (read September 24 2024)
- [3] Boeing CEO Talks ‘Digital Twin’ Era of Aviation. Retrieved from https://www.aviationtoday.com/2018/09/14/boeing-ceo-talks-digital-twin-era-aviation/ (read September 24 2024)
- [4] GE Vernova unveils new AI-based software to advance industrial sustainability and operations goals simultaneously. Retrieved from https://www.ge.com/news/press-releases/ge-vernova-unveils-new-ai-based-software-to-advance-industrial-sustainability-operations-goals (read September 24 2024)
Digital Marketing & Business Specialist